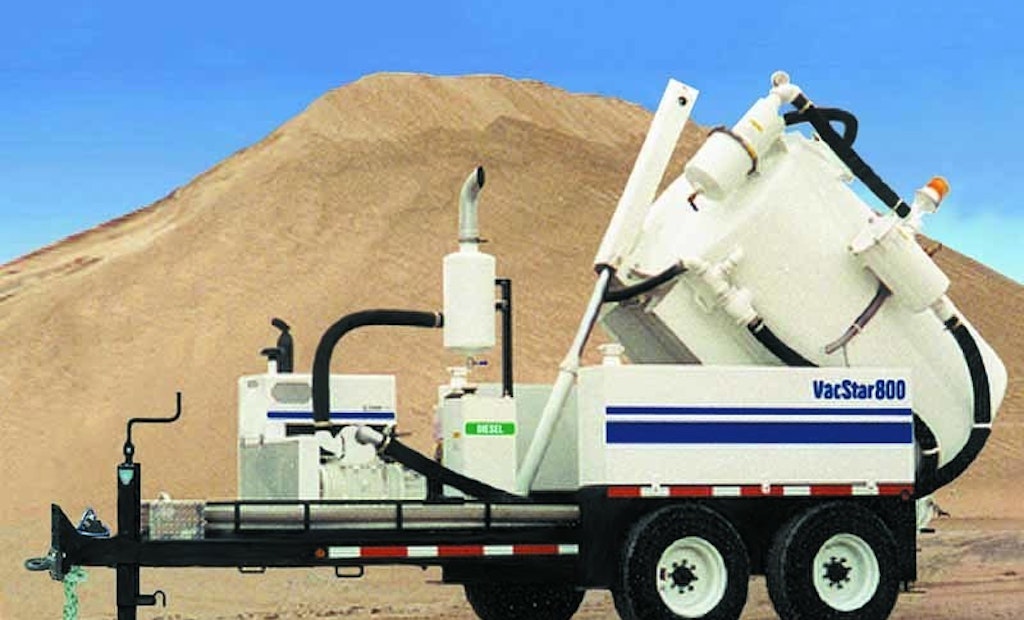
Interested in Cleaning?
Get Cleaning articles, news and videos right in your inbox! Sign up now.
Cleaning + Get AlertsVacuum excavation is a valuable tool in the water and wastewater world. And if you find yourself working a lot of jobs that need that vacuum power in a more compact package, a trailer-mounted unit is likely a part of your fleet.
Like any machine, proper maintenance goes a long way in keeping everything running smoothly. Keep the following advice in mind to ensure problem-free operation of your vacuum excavator.
1. Do a thorough prejob inspection
A good maintenance routine for any equipment begins with a prejob inspection. On trailer-mounted vacuum excavation units, start from the ground up, suggests Jerry Hatfield, training and warranty manager for Sewer Equipment Co. of America.
“Check the tires. Are they properly inflated? When you’re pulling these trailers down the road, many of them are very heavy whether they have a load or not.
They’re carrying a lot of equipment so proper inflation is important for both the operator and the safety of the motoring public. Check the wheel lug nuts. It’s such a simple thing to do and yet I would be willing to bet there are a lot of operators who don’t even keep a wrench that fits the trailer lug nuts with the rest of their equipment.”
Other items to check on a trailer unit include turn signal lights and any reflective markings to make sure they’re clean, intact and clearly visible. From there, operators should move on to the vacuum excavation machine itself and check items such as oil levels.
“What they do in the yard before even going to a job site is going to set the tone for either a really good day or a really bad day,” Hatfield says.
2. Trailer hitch tips
An important aspect of the prejob inspection that doesn’t come into play for full-size truck-mounted vacuum excavators is the trailer hitch. “The hitch system is probably the one point that doesn’t get enough attention on a trailer unit because you don’t have that on a truck,” Hatfield says. “But it’s critical because that’s what is pulling the unit down the road.”
Before leaving for a job site, check the hitch for any signs of wear.
“If it’s a ball hitch, you need to check the condition of the ball itself. Are there edges ground off of it, or does it have a crack? If it’s a pintle hitch, it’s a little different, but those should be looked at as well because they will crack from fatigue after awhile,” Hatfield says.
To prevent damage to the hitch system, Hatfield recommends not overloading the trailer and making sure it’s attached to the truck in a way that doesn’t overstress the hitch.
“Make sure the trailer is running relatively level so the tires are all carrying the load the same way,” he says. “Say the hitch on the trailer is high. If it’s a dual-axle trailer — and most units are — now you’re carrying a lot of weight on the rear axle that should be running on the front axle, and that puts a lot of additional strain on the hitch.”
3. Don’t neglect regular fluid checks
Engine oil and other fluids should be checked on a daily basis, Hatfield says.
“It’s really easy to do, but a lot of times it gets ignored,” he says. “A few quarts of oil is a lot cheaper than replacing an engine. Sometimes you get a person complaining about an engine failure. Well, did anyone bother to check anything in that unit before taking off to the job site?”
4. Other fluid-related tips
If it’s a hydroexcavation unit and you have water on board, Hatfield recommends keeping an eye on the condition of the water pump oil. “Make sure it’s not cloudy like there’s water in it because that degrades the lubrication of the oil,” he says. “That can cause the water pump to wear out very quickly.”
For the blower, check to make sure the oil is at the proper level as you would with other components but also be leery of adding too much oil.
“It can actually over-pressurize the oil chambers on some blowers out there and be just as bad as not having enough oil. The blower can fail because of that,” Hatfield says.
5. Service intervals
Follow manufacturer guidelines to gauge when to change out the fluids on your machine. Hatfield says a good rule of thumb is every 500 hours of operation.
“You might have a break-in period of 100 to 200 hours on a lot of your lubrication,” says Hatfield. “It depends on the component, but for engine oil, pump oil, blower oil and hydraulic oil, after that break-in period, many manufacturers will probably recommend about a 500-hour service interval to go through the entire unit.”
6. Adjust based on operating conditions
Of course, you might have to tweak your service schedule based on the type of environment you’re working in. Operators who live and work in a region that sees a cold winter will want to be mindful of water condensation affecting oils.
“That’s when it’s nice to change out the oil,” Hatfield says. “Some operators will change it in the spring and in the fall. That way they’re ready with new oil for winter and new oil for the summer. It’s a personal preference thing, but 500 hours is still a nice rule of thumb.”
In warmer climates, operators may not have to worry about condensation buildup as much, but running the unit too hard for too long can be an issue.
7. Take a break to avoid a breakdown
That’s a scenario in which the best maintenance can be as simple as not overworking the vacuum excavator. “In high-heat situations, hydraulic oils get pretty warm and engines run pretty hot,” Hatfield says.
The blower in particular is something to keep an eye on. Hatfield says operators should closely follow the manufacturer’s blower usage guidelines.
“Those guidelines will say something along the lines of run the blower at up to 75 percent of its max capacity for only this length of time before raising the boom to let some ambient air in to cool it down. Blowers will generate a lot of heat, and you don’t want a premature blower failure just because you were running it a bit too hard.”
8. Other things to watch for during operation
Hatfield says it’s a good practice to continue to monitor oil levels during the course of operation.
“It’s easy enough most of the time to keep an eye on it through things like sight glasses,” he says. “Even if you stop and break for lunch, it’s not a bad idea to go around and check oil levels before starting back up again. Oil is really the lifeblood that is keeping the unit going.”
Also get out the grease gun and apply grease to any areas as needed, such as drive shafts.
“A lot of it has to do with how intensely they’re operating,” Hatfield says. “An operator who does a couple of potholes and is maybe using the unit for an hour a day is a little different than a person who is out in the oilfields running it hard all day long.”
9. Grease liberally
Regularly greasing components is one of the top maintenance items that is overlooked, Hatfield says.
“I’ve had many customers with component failures in which it turned out just to be a lack of lubrication on a drive shaft,” he says. “A little bit of grease on a daily basis would fix a lot of problems.”
He recommends applying at least a quarter tube of grease per day on bearing surfaces. “The vacuum may actually pull some of the grease out past the seals,” he notes. “I’ve yet to see anyone overgrease a piece of equipment.”
10. Boom maintenance
Hatfield says out of all the components on a vacuum excavator, the boom rotation drive system may be the one that is especially important to grease regularly.
“Not only are you carrying the weight of the boom, you’re also carrying the weight of the vacuum — whatever material you’re pulling up into the debris tank is also creating weight. So it’s already under a lot of strain, plus it’s operating in a dirty environment. Invariably they’ll fail because of a lack of grease.”
When greasing the boom, it’s critical to rotate it as well.
“Many manufacturers will say grease, rotate it, grease, rotate it some more,” Hatfield says. “If you don’t do that, you’ll only get grease in one spot and it could very well fail on the opposite side of where the grease was applied.”