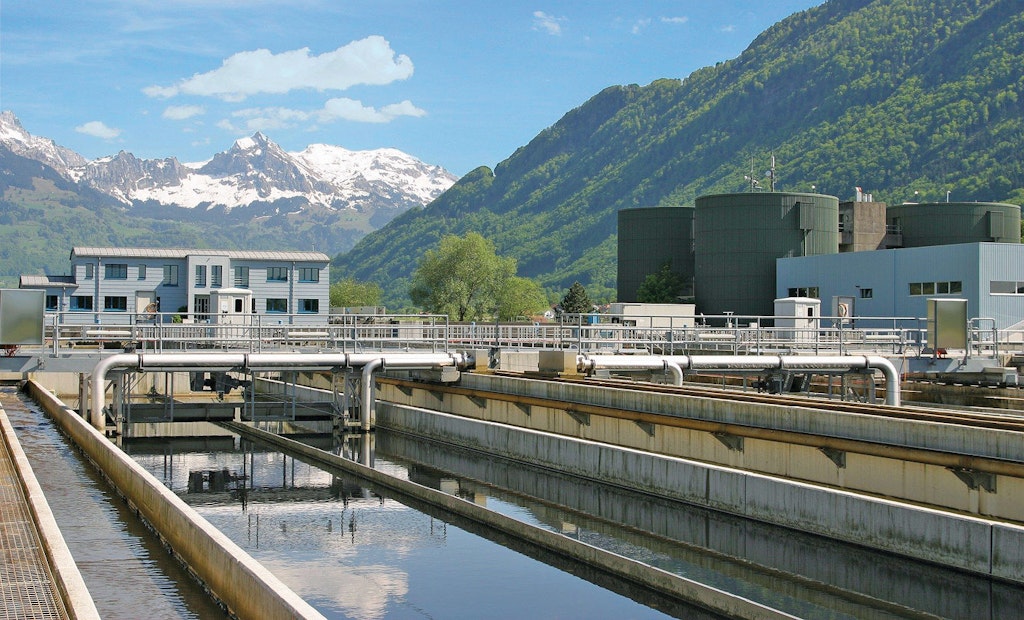
Monitoring hydrogen sulfide is critical for the safety of your crew. Even at concentrations below the toxic level, it can cause irritation of the eyes, nose and throat, headache, nausea, dizziness and loss of coordination.
Interested in Safety?
Get Safety articles, news and videos right in your inbox! Sign up now.
Safety + Get AlertsHydrogen sulfide (H2S) is a gas commonly found in wastewater applications, resulting from the decomposition of organic matter. It is toxic, combustible and can be corrosive. Effective monitoring — and choosing the appropriate measurement system — requires an understanding of why the data is being collected and how it is being used.
Hydrogen sulfide is a colorless gas that is often described as having the odor of rotten eggs when present in low concentrations. It is flammable and releases sulfur dioxide (SO2) when burned. It can be toxic at concentrations above approximately 300 ppm and is also corrosive to metals and concrete, in addition to other materials.
Origins
Hydrogen sulfide can be found in natural sources such as petroleum, natural gas and some well water, as well as industrial settings such as refineries, steel mills and wastewater treatment plants. In addition, it can be produced through the decomposition of organic materials by naturally occurring bacteria in areas with low oxygen concentrations, such as swamps, or underground through a process known as anaerobic digestion.
In wastewater collections systems and treatment plants, H2S is produced when anaerobic bacteria digest sulfates and organic material via the reduction reaction:
SO4-2 + organic material -> H2S + CO2
If oxygen is present, there is a balancing reaction by aerobic bacteria to oxidize the H2S:
H2S + 2O2 -> H2SO4
Potential problems
There are three important reasons to monitor H2S:
1. Health and safety issues — As mentioned, hydrogen sulfide can be toxic at concentrations above 300 ppm and is flammable; at higher concentrations, a mixture of H2S and air can be explosive. Even at concentrations below the toxic level, it can cause irritation of the eyes, nose and throat; headaches; nausea; dizziness; and loss of coordination. It is also heavier than air and can pose a hazard if it is allowed to accumulate in pits and other poorly ventilated places.
2. Public nuisance complaints — The rotten egg smell that accompanies H2S can often lead to complaints from residents near manholes, discharge points, treatment plants, landfills and other types of processing and manufacturing facilities.
3. Infrastructure damage — H2S is corrosive and can lead to the degradation of pipes, manholes, lift stations and pumping equipment.
Eliminating H2S
2S revolve around the management of >span class="s2">the anaerobic sulfate-reducing bacteria, or SRB, that are the source. First, there is a competing reaction that depends on oxygen to convert the hydrogen sulfide to sulfuric acid. Increasing the oxygen level via aeration can reduce the anaerobic reaction, enhance the competing reaction and reduce H2S levels.
Another method is to reduce the presence of the SRB via a biocide such as chlorine, alkalis or nitrites. The introduction of nitrates or anthraquinone can change the behavior of the SRB and reduce the formation of H2S. Finally, modifying the operation of the system (for example, introducing other friendly bacteria or speeding up flow rate) can suppress the activity of SRB.
Monitoring
There are a variety of methods to detect the presence of hydrogen sulfide. The simplest is the sense of smell. It’s actually possible to smell H2S at levels of less than 1-10 ppm; however, you would not want to be any place where the level was greater than 20 ppm for any period of time.
>span class="s3">of H2S including lead-acetate-coated test strips, colorimetric tubes and the Tutwiler method, which uses chemical titration. One of the most accurate methods is gas chromatography, but this requires a relatively large and expensive piece of equipment and may not be practical for use in the field.
Finally, there are electronic monitors that use small electrochemical sensors to detect H2S. These sensors use a specially treated sensing electrode along with an electrolyte; the incoming gas undergoes a chemical reaction at the sensing electrode that generates an electrical signal. These sensors typically employ a counter and/or reference electrode to provide a differential output signal that is only based on the concentration of the specific gas being measured.
One important consideration when using these sensors is that they have a finite operating time when used in the presence of hydrogen sulfide. Since they depend on an electrochemical reaction, there is an electrolyte that is converted as part of the reaction. Eventually, once all of the electrolyte is converted, the sensor can lose its ability to respond to H2S. When this happens, the sensor has to be regenerated by removing it from the monitoring location and placing it in a normal environment to allow it to recover. A good rule of thumb is that the sensor needs to spend an amount of time in the normal environment equal to the amount of time in the monitored environment to fully recover.
Selecting a monitoring system
When choosing a system to monitor H2S gas levels for a semipermanent installation (as opposed to a personal protective monitoring unit), there are several considerations to take into account:
1. What is the application and associated measurement range?
a. Odor control
b. Monitoring natural sources
c. Health and safety
d. Flammability/combustibility monitoring
e. Corrosion management
f. Treatment/remediation management
2. How often will a measurement be taken?
3. How long does the unit need to be left in place?
4. How much onboard data does the unit need to store?
5. What is the environment like?
6. Does the unit need a real-time display?
7. How will the data be retrieved?
8. Does the unit need any alarm output?
9. Does the unit need any real-time output?
In general, odor control applications, such as monitoring along a fence line or at the output of a scrubber, require the ability to measure at low levels, typically less than 5 ppm. Sample rates from once every 10 minutes to once per hour are commonly used. These are often temporary installations that may last a week or two and require storage for a few thousand data points.
Systems intended for health and safety monitoring would typically need a range up to 100-200 ppm — OSHA has set a ceiling of 20 ppm continuous with a maximum peak of 50 ppm for a maximum of 10 minutes during an eight-hour shift. This type of application would almost certainly require a real-time display and alarm with a sample rate of one to 10 minutes.
For longer-term projects such as monitoring for corrosion management or treatment, the ability to sense over a wider range, up to several thousand parts per million, may be required. These applications can involve monitoring in harsh, wet or high-humidity corrosive environments that require a robust instrument package with O-ring seals. Since these units could be left in place for long periods of time, large internal memory and battery life are required to allow extended operation.
To facilitate data retrieval, a wireless interface such as Bluetooth can make it possible to easily download data to a mobile device rather than relying on a hard-wired connection to a PC. For unattended data retrieval, a device with an internal cellular modem can automatically push data and alarms to eliminate the need to physically access the logger. Also, these longer-term installations will usually require multiple loggers so that they can be swapped in or out of service to allow recovery after extended use times.
Finally, some applications, such as dosing of a chemical to eliminate the SRB that generate H2S, will require an output signal to connect to an existing system. An H2S data logger that can provide an industry-standard 4-20mA current output allows the unit to provide a real-time output that can be tied into a SCADA system for equipment control, alarm activation and long-term historical data recording.
Terry Nagy is the engineering manager at CAS DataLoggers with more than 20 years of experience in measurement and instrumentation systems.