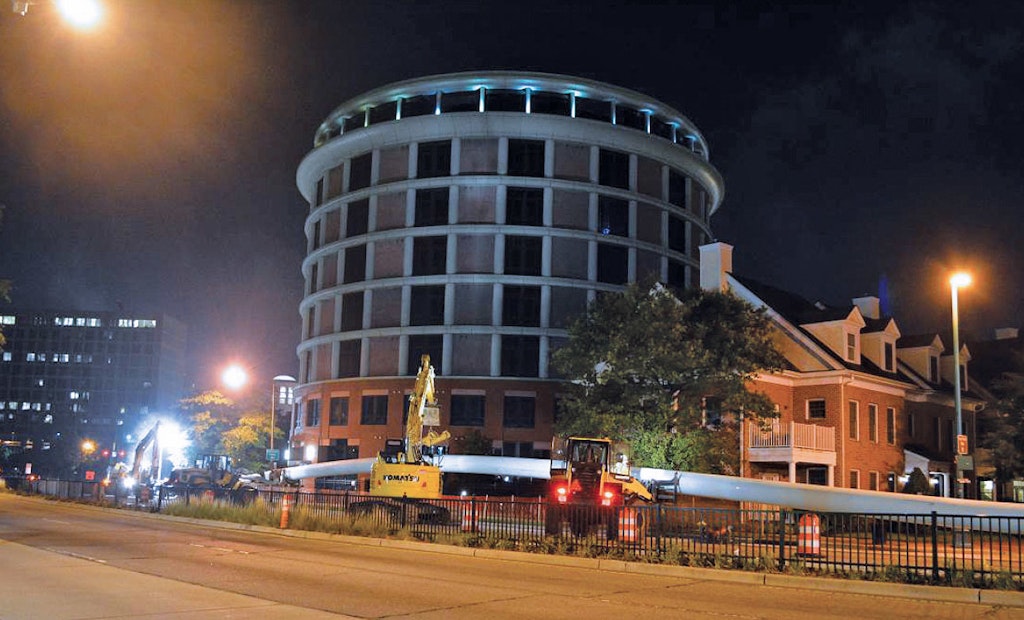
Nighttime HDD work took place adjacent to this condominium building, requiring steps to ensure there wasn’t too much ground vibration.
Interested in Rehab/Relining?
Get Rehab/Relining articles, news and videos right in your inbox! Sign up now.
Rehab/Relining + Get AlertsWhat do you get when you cross opencut with directional drilling and historical landmarks? The answer could be a recipe for disaster if something goes wrong.
The project was to replace a large segment of 36-inch prestressed concrete cylinder pipe force main in the downtown Norfolk, Virginia, area. The pipe was beyond its intended service and was starting to become a high-risk concern.
“Not only was it time for it to be prioritized for replacement, but it was also under an EPA consent order agreement,” says Will Gibson, project engineer for the engineering firm AECOM. “There were multiple reasons to get that pipe replaced or rehabilitated.”
The project originally was proposed as all opencut. During construction, however, the general contractor decided it was worth exploring alternative methods on a troublesome portion of the route. If opencut were to be used, it would affect more streets and a shopping mall and take longer to complete the project.
After several concepts were considered and eliminated, the contractor submitted a design-build proposal using a 1,000-linear-foot, 30-inch directional drill to keep the alignment straight and on its current path.
An aging pipe
The Hampton Roads Sanitation District owns and operates the large regional force main interceptor system and 13 wastewater treatment plants, providing service to 18 counties and cities and approximately 1.7 million residents in the Hampton Roads region of Virginia.
In 2011, the district began the South Trunk Sewer Section G Force Main Replacement Project to replace about 6,000 linear feet of a large-diameter force main, constructed in the 1940s, in downtown Norfolk.
AECOM began by studying and comparing alignment plans to navigate the new replacement 30-inch ductile iron pipe force main through the major and minor streets of Norfolk. It was determined that most of the new force main would be located along St. Paul’s Boulevard (running north-south), which is a heavily traveled roadway for commuters and residents.
During the design phase, the Norfolk Utilities and Public Works Departments prohibited any work through the Market Street and City Hall Avenue intersections along the force main route. These intersections were vital to commuter access to and from St. Paul’s Boulevard and Interstate 264, a major regional highway adjacent to downtown.
Trenchless crossings were explored at that time, but due to some construction projects in adjacent areas experiencing problematic crossings or ground settling, the city preferred finding opencut solutions around the intersections.
“We stayed along the major corridor, and then we had to dive off that corridor to get around those two major intersections to continue with an opencut alignment,” Gibson says.
The design was modified to align the force main down a small side street adjacent to Norfolk’s busiest shopping mall to avoid the intersections. The design through the tight corridor presented various challenges.
“Our restrictions on the contractor for that area were very tight,” Gibson says. “They could only work certain times of the year and certain times of the day, and a lot of it was confined to night work. There were a lot of stipulations there, which is why when the contractor got going, they wanted to take a look at HDD.”
Going with HDD
Early in the construction phase, the contractor, Tidewater Utility Construction, evaluated the challenges of the alignment and proposed several ideas to avoid the segment of opencut installation. After several concepts were considered and eliminated, Tidewater Utility Construction submitted a design-build proposal using a 1,000-linear-foot, 30-inch horizontal directional drill along St. Paul’s Boulevard, continuing with the overall alignment.
“At that point, AECOM and the general contractor had made enough headway, done enough good work and impressed the city enough that they were willing to allow us to propose that and take a look at HDD,” Gibson says. “So the HDD actually wasn’t initiated until we were in the middle of construction, which makes it kind of interesting.”
HDD still posed some challenges, however, especially with the tight working area.
“We were surrounded by very large buildings, the high-end shopping mall, the downtown Norfolk courts complex and then some high-end residential condos and town houses,” Gibson says. “We had everything that you could imagine around us. So even with HDD not having quite the staging requirements of a microtunnel, it’s still a lot of equipment to put out there.”
AECOM, Tidewater Utility Construction, and the directional drill contractor, Spring & Associates, were required to submit a detailed staging plan to the city and explain where each piece of equipment was going to be, what kind of lane shutdowns were expected and all of the impacts of those.
“There was quite a submittal to the city just for them to sign off on how we were going to stage this,” Gibson says.
Crews were able to keep much of the staging to a single lane. Equipment included the American Augers DD-210 directional drill, the control room and the Tulsa Rig Iron MCM 1000 mud recycler unit all in a single lane of traffic, along with the entry pit.
“During nonrush-hour times, we were able to take a second lane just to open up the workspace a little bit,” Gibson says.
Understanding history
Norfolk is a city rich with history dating back to the Colonial times of the 17th century. Understanding the city’s historical evolution was critical during the design of the proposed pipeline.
“If you look at the history of the city, the downtown area was actually a lot more water area than it is today,” Gibson says. “The reason is because in the 1800s, the city expanded their landmass into the Elizabeth River and they did this by pretty much taking a landfill mass and other materials and just dumping it into the water to create the land and build it out.”
Because of that, many areas of downtown Norfolk are not applicable to trenchless technologies.
“What we found out during some preliminary studies was that a lot of the things they threw in there were huge,” Gibson says. “They were big masses of brick and concrete, and all kinds of things that you probably would not want to drill through on a normal basis knowingly.”
There were other areas early in the design phase where they looked at doing a trenchless cross, only to find out the land had been built out and there was no guarantee of avoiding obstacles.
“We had to convince the city in some areas to stick with the opencut and not go with trenchless because of those obstacles,” Gibson says. “So this project actually ended up being a mix of microtunneling at the start, opencut and then HDD and then opencut again.”
One of the more substantial historical considerations was a church located along the directional drill route. The church, the oldest structure in Norfolk, was constructed in the 1730s and is on the National Register of Historic Places.
“The church was probably the most high-profile structure that we were working very closely to,” Gibson says. “It was obviously a very big concern, and we believe structurally that the church is kind of a slab-on-grade design. With anything HDD related, you always worry about the inadvertent returns, and with our alignment being within 100 feet of that church and the brick wall surrounding the church, we were concerned that if inadvertent returns went toward the church, possibly under or close to the structure, we would undermine it and have some settling issues.”
AECOM developed a monitoring plan, which included topographic survey, vibration monitoring and installation of monitoring wells. The topographic survey was a way to document the before and after elevations of above-ground features.
“The monitoring wells we drilled were about 12 feet down and we put in a perforated PVC pipe, and we did this about every 50 feet along the church, which is about a 500-foot span,” Gibson says. “They were designed as an early warning system. So if we had an inadvertent return heading toward the church, the idea is that those fluids would go up the bored wells and we would see fluid come out of them. If we did see that, we could shut down the operations and try to mitigate any returns heading toward the church and go with our contingency plans at that point.”
Wrapping up
Fusing of the pipe took place concurrently with the drilling activities, and a full stringout was done prior to pipe-pull efforts. The city and the contractors agreed to complete the pullback in the nighttime hours.
Although the HDD installation accounted for just 1,000 feet of pipe out of the project’s total 6,000 feet, the impact was substantial.
“The overall results by doing the HDD were outstanding,” Gibson says. “We avoided the opencut, and we avoided, by going under those two intersections, impacting traffic. We also credit the HDD with shaving about five months off the construction time.”
The early finish saved the city approximately a million dollars on a $10 million-dollar project.
“The extra precautions that we took with the monitoring wells and just everybody being on the same page in terms of communicating and having the inspectors where they needed to be at the right time — all that quality assurance/quality control couldn’t have gone better,” Gibson says. “It’s what prevented anything from going wrong.”