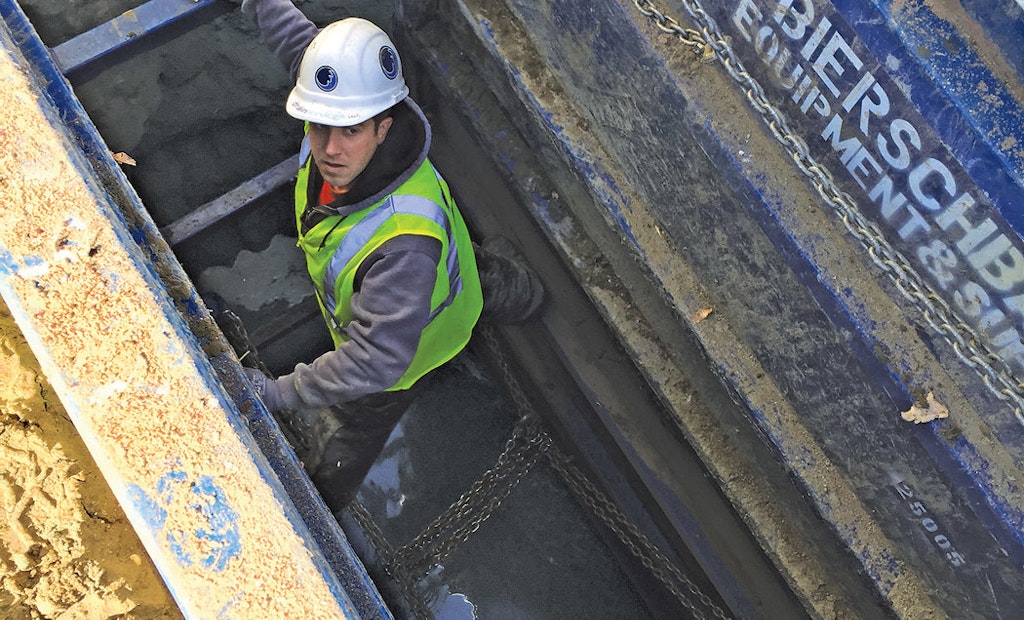
Any trench greater than 5 feet deep must have some type of collapse prevention. The method used for prevention depends on two factors: trench layout and soil conditions.
Eight service workers died in trenching accidents last April. Staying safe requires more than following regulations: It takes a thorough understanding of the tools available.
“Not everything that these guys are confronted with is in the rulebooks,” says Jim Sullivan, president...