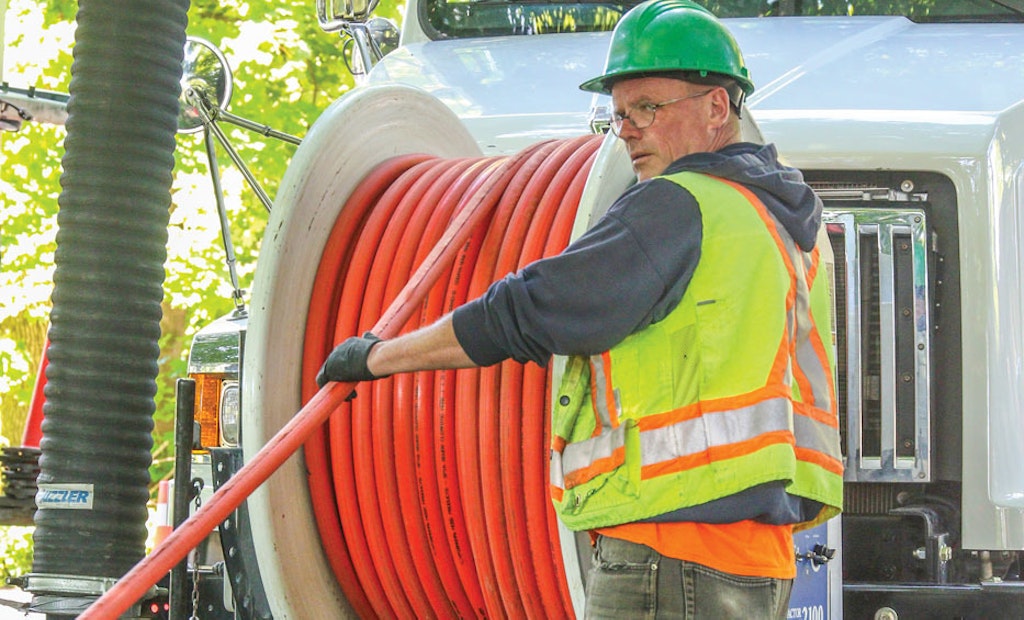
Proper training is the key to an efficient and effective cleaning operation. It starts with thorough knowledge of the equipment and how it functions.
Efficiency is often the bane of in-house municipal cleaning operations, but for those utilities seeking optimization among their cleaning crews, good news is here in the form of operator training.
One of the most comprehensive cleaner training programs out there is offered by...