If you’re in the process of choosing a new inspection or rehabilitation system, you should calculate the true cost of ownership. Expenses must be weighed against the brand’s productivity potential in order to assess the true cost of ownership and return on investment. Spend some time thinking about the following cost and productivity factors, comparing each brand and/or technology.
Factors to consider
Initial purchase price — The initial price is important, but it is by no means the only factor. Don’t forget that there are many manufacturers and dealers who will work with municipalities and contractors to get them the equipment they need and stay within a reasonable budget.
Production rates — Each piece of equipment has its own capabilities. Do you expect to inspect the estimated national average of 1,500 feet per day, or will the equipment you choose inspect up to 5,000 feet per day. Technologies exist that can easily inspect two to three times more per day than traditional CCTV systems. They have a higher initial purchase price, but lower operational costs due to this high production rate.
Employee wages, benefits and salaries — Will the equipment require an increase or a decrease in labor to complete your project on time? Equipment with high productivity rates can reduce your employee cost exposure allowing you to inspect more with fewer dedicated employees. Equipment that is safer and easier to operate can also reduce employee stress.
Vehicle maintenance costs — What do you typically spend to own, license, run and maintain a vehicle? Systems with high productivity can reduce the size of your fleet, reducing your cost.
Repair cost — Is the system going to be costly to repair? How often will it break down? All systems are susceptible to damage, but a well-designed system can reduce recurring repair costs. If you save $10,000 on the initial purchase price, you may find yourself paying well over that each year in repair and maintenance costs.
Lost time due to repairs — Contractors lose money and municipalities get behind schedule when equipment breaks down. If equipment does not break down, it’s in the field paying for itself and not sidelining personnel.
Features — Does the system provide deliverables that allow the contractor to charge more for their services compared to the competition, and the owner to make better decisions regarding their infrastructure?
Product life cycle — Will this equipment last 10 years or three? Is the system ready for digital output? Consumer electronic products have a notoriously short life cycle, and if the manufacturer chooses to use off-the-shelf components, you may find yourself with a system that is outdated in a few years.
Making decisions
It’s critical that contractors and municipalities make educated purchase decisions. Choosing the right equipment can make your life easier, increase your effectiveness and decrease your costs, but you must be cognizant of product quality and the benefits it can provide. Look at the total cost of ownership that a piece of equipment has over the course of its expected life cycle and make purchase decisions based on the true costs.
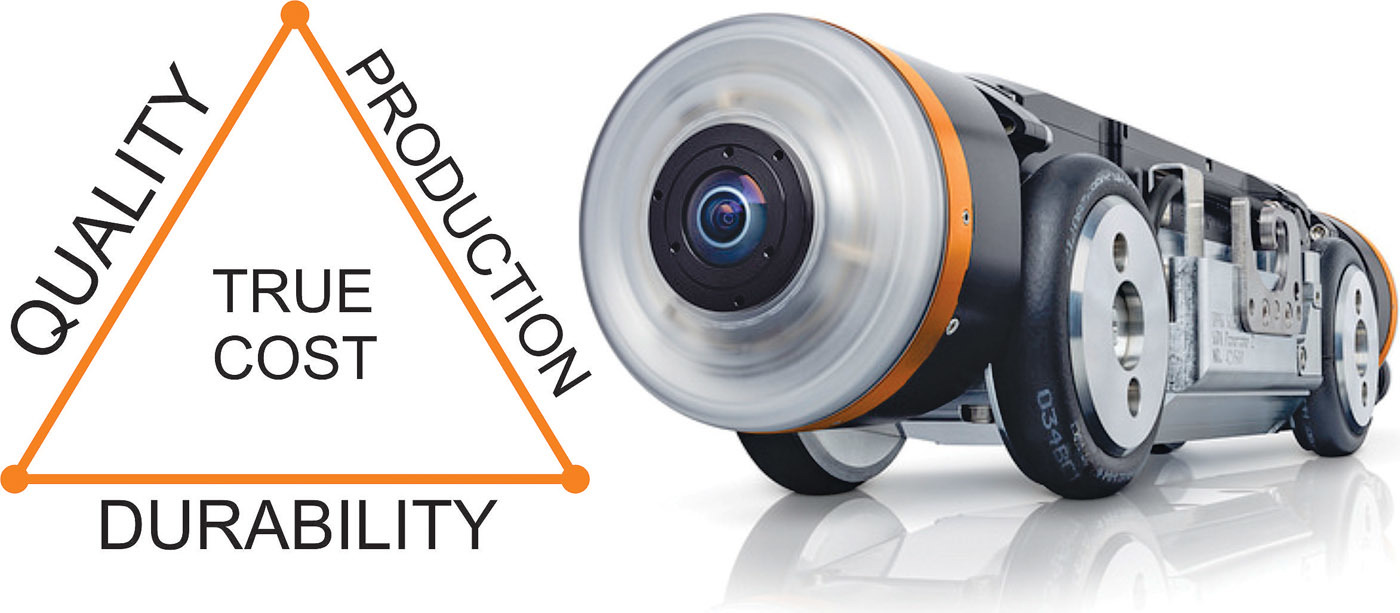
RapidView LLC has created business partnerships with several manufacturers of high-quality sewer pipeline maintenance products, including its primary product line from IBAK Helmut Hunger GmbH & Co. KG of Kiel, Germany, a manufacturer of high-quality CCTV pipeline inspection systems since 1957. Rapidview LLC imports, distributes and services the complete IBAK camera inspection product line, within North America, from its facility in Rochester, Indiana.
800-656-4225 | info@rapidview.com | www.rapidview.com